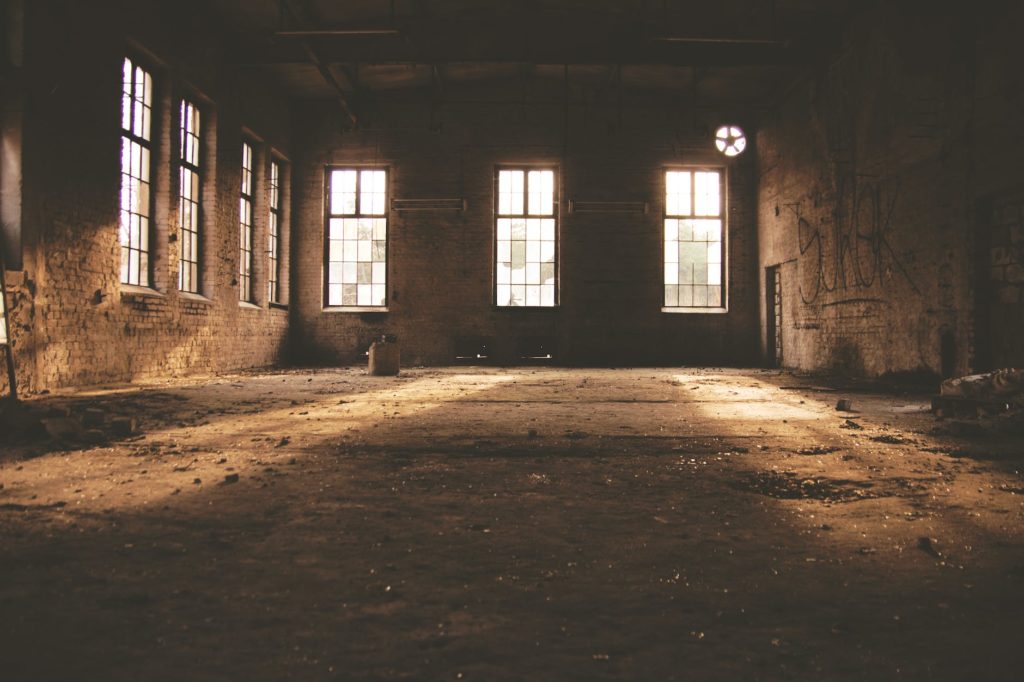
Zrozumienie i wykorzystanie wskaźnika OEE, czyli efektywności całkowitej maszyn, to klucz do osiągnięcia maksymalnej wydajności w procesach produkcyjnych. Dzięki temu narzędziu można dokładnie monitorować i oceniać wykorzystanie czasu pracy, jakość produkcji oraz skuteczność urządzeń. Pozwala to identyfikować obszary wymagające poprawy i podejmować odpowiednie działania w celu zwiększenia efektywności całego systemu. Wiedza na temat OEE jest niezbędna dla każdego przedsiębiorstwa dążącego do optymalizacji swoich operacji.
Wskaźnik OEE – kluczowy miernik wydajności produkcji
Wskaźnik efektywności całkowitej (OEE) jest jednym z najważniejszych mierników wydajności produkcji. Jest to wskaźnik, który mierzy stopień, w jakim maszyny i linie produkcyjne są wykorzystywane w sposób optymalny. OEE łączy trzy główne składniki: dostępność, wydajność i jakość.
Dostępność odnosi się do czasu rzeczywistego, w którym maszyna jest gotowa do pracy. W przypadku awarii lub konserwacji maszyny, czas niedostępności wpływa negatywnie na wartość OEE.
Wydajność odzwierciedla tempo produkcji względem standardowego tempa pracy. Jeśli maszyna działa poniżej swojej maksymalnej prędkości lub występują opóźnienia procesowe, wpływa to na wynik OEE.
Jakość dotyczy ilości produktów spełniających wymagania jakościowe. Jeśli często pojawiają się defekty lub odpadki podczas procesu produkcyjnego, wartość OEE spada.
Rozkład składników OEE – dostępność, wydajność i jakość
Aby dokładnie zrozumieć wskaźnik OEE, ważne jest zrozumienie rozkładu składników: dostępności, wydajności i jakości. Dostępność mierzy czas rzeczywisty, w którym maszyna jest gotowa do pracy. Wydajność odzwierciedla tempo produkcji względem standardowego tempa pracy. Jakość dotyczy ilości produktów spełniających wymagania jakościowe.
Analiza tych trzech składników pozwala identyfikować obszary problematyczne i potencjalne źródła strat produkcyjnych. Na przykład, jeśli dostępność jest niska, może to oznaczać problemy z konserwacją lub częstymi awariami maszyn. Jeśli wydajność spada, należy zbadać przyczyny opóźnień procesowych lub ograniczeń prędkości maszyny.
Z kolei niska jakość może wynikać z problemów technologicznych lub niedoskonałości w procesie produkcyjnym. Analiza rozkładu składników OEE umożliwia lepsze zrozumienie efektywności produkcji oraz identyfikację obszarów wymagających poprawy.
Dlaczego OEE jest ważne – korzyści dla przedsiębiorstwa
Wskaźnik OEE ma kluczowe znaczenie dla przedsiębiorstwa ze względu na wiele korzyści, jakie niesie ze sobą. Po pierwsze, OEE pozwala na identyfikację i eliminację strat produkcyjnych, co prowadzi do zwiększenia wydajności i rentowności.
Po drugie, poprzez monitorowanie wskaźnika OEE można lepiej zarządzać czasem pracy maszyn oraz planować konserwacje lub naprawy w sposób optymalny. To przyczynia się do zmniejszenia awarii i uniknięcia nieplanowanych przestojów produkcyjnych.
Po trzecie, OEE dostarcza danych potrzebnych do podejmowania decyzji strategicznych dotyczących inwestycji w nowe technologie lub modernizacji linii produkcyjnej. Dzięki temu przedsiębiorstwo może utrzymać konkurencyjność na rynku.
Obliczanie OEE – krok po kroku
Aby obliczyć wartość wskaźnika OEE, należy uwzględnić trzy składniki: dostępność (D), wydajność (P) i jakość (Q). Obliczenie odbywa się według wzoru:
- OEE = D x P x Q
Dostępność jest obliczana jako stosunek czasu rzeczywistego pracy maszyny do całkowitego czasu możliwego działania maszyny. Wydajność to stosunek rzeczywistej prędkości produkcji do maksymalnej prędkości maszyny. Jakość jest obliczana jako stosunek ilości produktów spełniających wymagania jakościowe do ogólnej produkcji.
Obliczenie OEE pozwala na monitorowanie efektywności produkcji w czasie i identyfikację obszarów wymagających poprawy.
Interpretacja wyników OEE – co mówi o efektywności produkcji?
Wartość wskaźnika OEE można interpretować jako procentowy udział czasu, w którym maszyna była wykorzystywana w sposób optymalny. Im wyższa wartość OEE, tym bardziej efektywne są procesy produkcyjne.
Na przykład, jeśli wartość OEE wynosi 80%, oznacza to, że maszyna była wykorzystywana tylko przez 80% dostępnego czasu. Pozostałe 20% to stracony czas z powodu awarii, konserwacji lub innych przestojów produkcyjnych.
Dzięki interpretacji wyników OEE można dokładnie określić źródła strat i podjąć działania mające na celu ich eliminację. Wyższa wartość wskaźnika OEE przekłada się na większą rentowność przedsiębiorstwa oraz lepszą konkurencyjność na rynku.
Poprawa wskaźnika OEE – strategie i najlepsze praktyki
Aby poprawić wskaźnik OEE, istnieje wiele strategii i najlepszych praktyk, które można zastosować. Jedną z nich jest regularne monitorowanie maszyn i linii produkcyjnych w celu szybkiego wykrywania awarii lub problemów technologicznych.
Ważne jest również przeprowadzanie regularnych konserwacji oraz szkoleń dla personelu odpowiedzialnego za obsługę maszyn. Dzięki temu można zapobiegać awariom i utrzymać maszyny w optymalnym stanie pracy.
Innym sposobem na poprawę OEE jest analiza danych dotyczących czasów przestojów oraz identyfikacja ich przyczyn. Na podstawie tych informacji można wprowadzać zmiany mające na celu eliminację strat produkcyjnych.
Wdrożenie OEE w zakładzie produkcyjnym – wykorzystanie potencjału efektywności
Wdrożenie wskaźnika OEE w zakładzie produkcyjnym wymaga odpowiedniej organizacji procesów oraz zbierania danych dotyczących dostępności, wydajności i jakości. Ważne jest również zaangażowanie zarządu przedsiębiorstwa oraz personelu odpowiedzialnego za produkcję.
Po zebraniu danych należy je analizować i podejmować działania mające na celu eliminację źródeł strat. Warto także prowadzić regularne raportowanie wyników OEE, aby monitorować postępy i podejmować dalsze działania.
Wdrożenie OEE pozwala na wykorzystanie pełnego potencjału efektywności maszyn i linii produkcyjnych oraz przyczynia się do zwiększenia wydajności produkcji i rentowności przedsiębiorstwa.