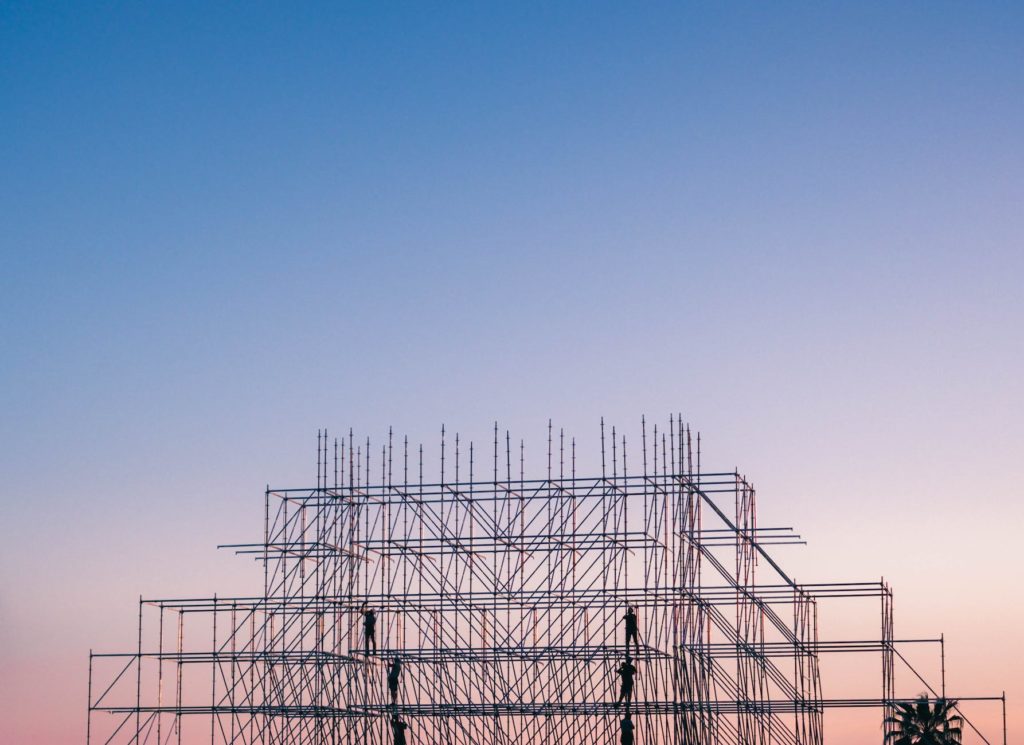
Przemysłowy świat nieustannie się rozwija, a wraz z nim ewoluują również systemy zarządzania produkcją. Od początków przemysłowej rewolucji do dzisiejszych czasów, historia tych systemów jest pełna kluczowych etapów i innowacji. Począwszy od prostych metod ręcznego planowania produkcji, poprzez wprowadzenie maszyn parowych i linii montażowych, aż po nowoczesne technologie informatyczne – każdy krok w rozwoju miał ogromny wpływ na efektywność i organizację procesu produkcyjnego. Warto poznać historię oraz kluczowe etapy tej fascynującej ewolucji.
Początki zarządzania produkcją przed rewolucją przemysłową
Przed rewolucją przemysłową, procesy produkcyjne były zazwyczaj prowadzone w sposób chaotyczny i niezorganizowany. Pracownicy często wykonywali swoje zadania według własnego uznania, co prowadziło do niskiej efektywności i jakości produktów. Brak standardowych procedur oraz brak nadzoru spowodowały, że produkcja była wolna i mało skuteczna.
Jednakże, już w starożytności można było zaobserwować pewne formy organizacji pracy. Na przykład w Egipcie faraonowie stosowali system podziału pracowników na specjalistów zajmujących się konkretnymi etapami produkcji np. budowy piramid czy też statków. W czasach średniowiecza również istniały warsztaty rzemieślnicze, gdzie mistrzowie kierowali pracą uczniów i czeladników.
Niemniej jednak to dopiero rewolucja przemysłowa w XVIII wieku dała początek nowoczesnemu zarządzaniu produkcją. Wynalezienie maszyn parowych oraz rozwój fabryk spowodowały potrzebę wprowadzenia bardziej zorganizowanego podejścia do zarządzania procesami produkcyjnymi.
Pierwszym kluczowym etapem ewolucji systemów zarządzania produkcją była standaryzacja procesów. Wprowadzenie standardowych procedur i instrukcji pracy pozwoliło na zwiększenie efektywności oraz jakości produktów. Pracownicy musieli przestrzegać określonych reguł i wykonywać swoje zadania w sposób spójny, co zapewniało większą kontrolę nad produkcją.
Kolejnym ważnym aspektem było wprowadzenie podziału pracy. Zamiast jednego pracownika wykonującego cały proces produkcyjny, poszczególne etapy zostały rozdzielone pomiędzy różnych specjalistów. Dzięki temu każdy mógł skupić się na swojej konkretnej roli, co przyczyniło się do wzrostu wydajności i osiągnięcia lepszych wyników.
Ostatnim kluczowym elementem tego okresu był rozwój masowej produkcji. Wykorzystanie maszyn parowych umożliwiło szybsze i bardziej efektywne wytwarzanie towarów. Powstałe fabryki mogły produkować duże ilości produktów o stałej jakości, co otworzyło drogę do dalszego rozwoju zarządzania produkcją w kolejnych dekadach.
Rewolucja przemysłowa – wpływ na rozwój zarządzania produkcją
Rewolucja przemysłowa, która miała miejsce w XVIII i XIX wieku, miała ogromny wpływ na rozwój zarządzania produkcją. Wprowadzenie maszyn parowych oraz mechanizacji procesów produkcyjnych spowodowało znaczne zwiększenie wydajności i możliwości produkcyjnych.
Jednym z kluczowych aspektów rewolucji przemysłowej było wprowadzenie linii montażowej. Henry Ford był pionierem tego podejścia, które polegało na podziale procesu produkcyjnego na serię prostych czynności wykonywanych przez różnych pracowników. Dzięki temu można było osiągnąć większą efektywność i szybkość produkcji.
Kolejnym ważnym elementem była standaryzacja części. Poprzez opracowanie standardowych komponentów, które mogły być stosowane we wszystkich produktach danej firmy, możliwe stało się masowe wytwarzanie towarów o niższych kosztach. To otworzyło drogę do powstania nowych gałęzi przemysłu oraz wzrostu konkurencyjności przedsiębiorstw.
Innowacje technologiczne, takie jak telegraf czy telefon, również odegrały istotną rolę w rozwoju zarządzania produkcją. Komunikacja między różnymi działami fabryki stała się łatwiejsza i bardziej efektywna, co przyczyniło się do lepszego koordynowania procesów produkcyjnych.
Wpływ rewolucji przemysłowej na rozwój zarządzania produkcją był ogromny. Nowe technologie i metody pracy otworzyły drogę do dalszych innowacji oraz rozwoju systemów zarządzania, które były niezbędne w coraz bardziej złożonym środowisku produkcyjnym.
Wprowadzenie nauki do zarządzania produkcją – teoria naukowa Fredericka Taylora
Fredrick Taylor jest uważany za jednego z pionierów nowoczesnego zarządzania produkcją. Jego teoria naukowa oparta była na badaniu i analizie procesów produkcyjnych w celu znalezienia najbardziej efektywnych metod pracy.
Jednym z kluczowych elementów jego teorii było wprowadzenie standaryzacji ruchów. Taylor doszedł do wniosku, że każdy ruch wykonywany przez pracownika może być zoptymalizowany, aby osiągnąć maksymalną wydajność. Poprzez analizę czasu trwania poszczególnych czynności oraz eliminację zbędnych ruchów można było skrócić czas wykonania zadania i zwiększyć ilość produktów wykonanych w tym samym czasie.
Innym ważnym aspektem jego teorii było wprowadzenie selekcji pracowników. Taylor uważał, że aby osiągnąć maksymalną wydajność, należy dobierać odpowiednich pracowników do konkretnych zadań. Każdy powinien być przeszkolony i posiadać umiejętności niezbędne do wykonania danej pracy.
Również motywacja pracowników była kluczowym elementem teorii Taylora. Poprzez wprowadzenie systemu premiowego za osiągnięcie określonych celów produkcyjnych, można było zachęcić pracowników do większego zaangażowania i wysiłku w wykonywaniu swoich obowiązków.
Teoria naukowa Fredericka Taylora odegrała istotną rolę w rozwoju zarządzania produkcją. Jego metody badawcze oraz podejście skoncentrowane na efektywności stały się podstawą dla dalszych innowacji i rozwoju dziedziny zarządzania produkcją.
Powstanie lean manufacturing – prowadzenie filozofii Just-in-Time
Filozofia Just-in-Time (JIT) jest jednym z najważniejszych aspektów lean manufacturing, które zostało wprowadzone przez japońskie przedsiębiorstwa w latach 70. XX wieku. Celem JIT jest minimalizowanie marnotrawstwa poprzez dostarczanie produktu dokładnie wtedy, gdy jest potrzebny.
Jednym z kluczowych elementów JIT jest redukcja zapasów. Tradycyjne podejście polegało na gromadzeniu dużych ilości surowców i gotowych produktów, co generowało koszty magazynowania oraz ryzyko przestarzałości. W przypadku filozofii Just-in-Time, dostawy są dokonywane w odpowiednich ilościach bez konieczności przechowywania nadmiarowych zapasów.
Kolejnym ważnym aspektem jest eliminacja marnotrawstwa. Poprzez analizę procesu produkcyjnego można identyfikować czynności, które nie dodają wartości dla klienta i eliminować je. To prowadzi do większej efektywności oraz oszczędności czasu i zasobów.
Ważną częścią JIT jest również ciągły rozwój pracowników. Pracownicy są zachęcani do zgłaszania pomysłów dotyczących poprawy procesu produkcyjnego. Dzięki temu każdy ma wpływ na doskonalenie systemu pracy i wzrost wydajności.
Filozofia Just-in-Time stała się fundamentem lean manufacturing, który obecnie jest szeroko stosowany w wielu branżach. Jego celem jest maksymalizowanie wartości dla klienta przy minimalnych nakładach zasobów, co przyczynia się do większej konkurencyjności przedsiębiorstw.
Era systemów informatycznych – od MRP do MRPII
W latach 60. i 70. XX wieku wprowadzenie komputerów do zarządzania produkcją otworzyło nową erę w rozwoju systemów zarządzania produkcją. Pierwszymi zastosowaniami były systemy Material Requirements Planning (MRP), które miały na celu optymalizację planowania zapotrzebowania na materiały.
Systemy MRP opierają się na analizie struktury wyrobów, czyli hierarchicznym przedstawieniu relacji między różnymi elementami produktu. Dzięki temu można określić, jakie ilości poszczególnych części są potrzebne do produkcji danego wyrobu oraz kiedy powinny być dostępne.
Kolejnym etapem było wprowadzenie systemów Manufacturing Resource Planning (MRPII). Oprócz planowania zapotrzebowania na materiały, MRPII obejmował również inne aspekty zarządzania produkcją, takie jak harmonogramowanie zadań produkcyjnych, kontrola jakości czy też zarządzanie magazynem.
Dzięki rozwinięciu technologii informatycznych możliwe stało się bardziej kompleksowe i dokładniejsze planowanie procesów produkcyjnych. Systemy MRP i MRPII przyczyniły się do poprawy efektywności oraz kontroli nad produkcją, co było niezbędne w coraz bardziej złożonym środowisku produkcyjnym.
Obecnie, systemy informatyczne odgrywają kluczową rolę w zarządzaniu produkcją. Wraz z rozwojem technologii, powstają nowe narzędzia i metody wspomagające procesy produkcyjne oraz umożliwiające lepsze monitorowanie i analizowanie danych.
Współczesne systemy zarządzania produkcją – ERP i MES
Współczesne systemy zarządzania produkcją to głównie Enterprise Resource Planning (ERP) oraz Manufacturing Execution System (MES). Obie te platformy mają na celu usprawnienie procesów produkcyjnych poprzez integrację różnych dziedzin działalności przedsiębiorstwa.
System ERP obejmuje wiele modułów funkcjonalnych, takich jak planowanie zapotrzebowania na materiały, kontrola jakości, zarządzanie magazynem czy też finanse. Dzięki temu wszystkie informacje dotyczące produkcji są dostępne w jednym miejscu, co ułatwia podejmowanie decyzji oraz koordynację działań między różnymi działami firmy.
MES natomiast skupia się na kontrolowaniu i monitorowaniu procesów produkcyjnych w czasie rzeczywistym. Pozwala on na zbieranie danych dotyczących wydajności maszyn, czasu cyklu produkcji czy też jakości wyrobów. Dzięki temu można szybko reagować na ewentualne problemy i podejmować działania naprawcze.
Współczesne systemy zarządzania produkcją są niezbędne w coraz bardziej złożonym środowisku produkcyjnym. Integracja różnych dziedzin działalności oraz dostęp do aktualnych danych pozwala przedsiębiorstwom efektywnie zarządzać procesami produkcyjnymi i osiągać lepsze wyniki finansowe.
Digitalizacja i przyszłość – nowe technologie i zarządzanie produkcją 4.0
Obecnie, digitalizacja odgrywa kluczową rolę w rozwoju zarządzania produkcją. Nowe technologie takie jak sztuczna inteligencja, internet rzeczy czy big data analytics umożliwiają jeszcze większą automatyzację procesów oraz analizowanie ogromnej ilości danych generowanych przez systemy produkcyjne.
Jedną z głównych koncepcji jest Industry 4.0, która zakłada pełną integrację wszystkich elementów procesu produkcyjnego – od surowca do gotowego produktu. Systemy cyber-fizyczne pozwalają na komunikację między maszynami oraz wymianę informacji w czasie rzeczywistym, co prowadzi do większej elastyczności i efektywności produkcji.
Wraz z rozwojem sztucznej inteligencji, możliwe staje się wykorzystanie algorytmów do optymalizacji procesów produkcyjnych. Systemy są w stanie analizować dane i podejmować decyzje na podstawie wcześniejszych wzorców oraz prognoz. To pozwala na szybszą reakcję na zmiany rynkowe oraz minimalizację ryzyka błędnych decyzji.
Analiza big data również odgrywa coraz większą rolę w zarządzaniu produkcją. Dane generowane przez systemy produkcyjne mogą być analizowane w celu identyfikacji trendów, wykrywania anomalii czy też doskonalenia procesów. Dzięki temu przedsiębiorstwa mają lepsze narzędzia do podejmowania strategicznych decyzji i poprawiania swojej konkurencyjności.
Zarządzanie produkcją 4.0 to przyszłość, która już teraz jest obecna w wielu firmach na całym świecie. Digitalizacja i nowe technologie umożliwiają osiągnięcie jeszcze większej efektywności, elastyczności oraz jakości produktów, co jest kluczowe dla sukcesu przedsiębiorstw w dynamicznym otoczeniu biznesowym.