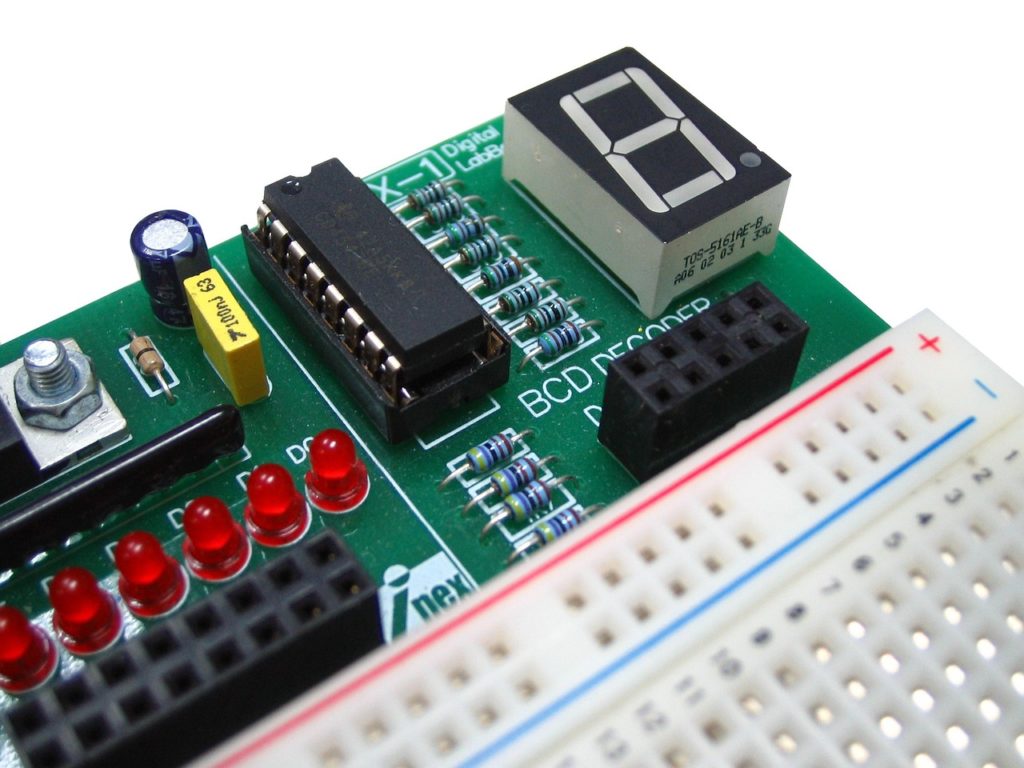
Jakie są podstawowe kroki projektowania schematu i układu, które stanowią podstawę dla produkcji płytek drukowanych?
Projektowanie schematu i układu to kluczowe etapy w produkcji płytek drukowanych. Pierwszym krokiem jest stworzenie schematu elektrycznego, który przedstawia połączenia między poszczególnymi elementami na płycie. W tym celu należy wykorzystać specjalne oprogramowanie CAD (Computer-Aided Design), które ułatwia projektowanie.
Kolejnym krokiem jest zaplanowanie rozmieszczenia elementów na płycie oraz ich połączeń za pomocą ścieżek miedzianych. Ważne jest tu uwzględnienie wymiarów płytki oraz miejsca, w którym będzie ona montowana. Projektant musi również zwrócić uwagę na poprawność działania układu oraz jego niezawodność.
Po stworzeniu schematu i układu następuje proces generowania plików GERBER, które zawierają informacje o warstwach miedziowych, otworach dla elementów oraz innych ważnych parametrach technicznych. Te pliki są niezbędne do wykonania płyty drukowanej.
Następnie przystępuje się do tworzenia samej płyty drukowanej przy użyciu specjalnej maszyny CNC (Computer Numerical Control). Maszyna ta korzysta z plików GERBER i wycinając odpowiednie kształty z laminatu pokrytego miedzią tworzy gotową płytę drukowaną.
Podsumowując, projektowanie schematu i układu to kluczowy etap w produkcji płytek drukowanych. Wymaga on precyzji oraz znajomości specjalistycznego oprogramowania CAD. Dzięki temu możliwe jest stworzenie niezawodnego układu elektronicznego, który będzie działał zgodnie z założeniami projektowymi.
Jakie są wymagane pliki i formaty potrzebne do produkcji PCB?
Produkcja płytek drukowanych (PCB) wymaga kilku plików i formatów, które są niezbędne do wykonania projektu. Pierwszym z nich jest plik schematu elektrycznego w formacie CAD. Ten plik zawiera informacje o połączeniach między elementami oraz ich umiejscowieniu na płytce.
Kolejnym ważnym plikiem jest lista materiałowa (BOM), która zawiera spis wszystkich elementów potrzebnych do produkcji PCB. W tym dokumencie znajdują się również informacje o ilości każdego elementu, jego wartości oraz specyfikacji technicznej.
Do produkcji PCB konieczny jest także plik graficzny w formacie Gerber lub ODB++. Ten format określa miejsca przewodzące na płytce oraz ścieżki połączeń między nimi. Plik ten musi być dokładnie dopasowany do wymiarów płytki i uwzględniać wszelkie szczegóły dotyczące otworów montażowych czy warstw izolacyjnych.
Innym ważnym dokumentem jest rysunek mechaniczny (Mechanical Drawing), który przedstawia fizyczne wymiary całej płytki drukowanej, jej kształt oraz pozycję otworów montażowych. Dokument ten ma kluczowe znaczenie dla procesu produkcyjnego, ponieważ dzięki niemu można zaprogramować maszyny odpowiedzialne za cięcie i wiercenie płytek.
Ostatnim, ale nie mniej ważnym plikiem jest plik testowy (Test File), który zawiera informacje o punktach testowych na płytce. Ten dokument pozwala na przetestowanie poprawności działania PCB i wykrycie ewentualnych błędów lub uszkodzeń.
Jakie są techniki prototypowania PCB?
Prototypowanie PCB to proces tworzenia wstępnej wersji płytki drukowanej, która zostanie użyta do testowania i oceny funkcjonalności projektu. Istnieje wiele technik prototypowania PCB, które pozwalają na szybkie i skuteczne tworzenie prototypów.
Jedną z popularnych technik jest frezowanie CNC. Polega ona na usuwaniu materiału z płytki za pomocą specjalnego narzędzia obrabiającego. Ta metoda pozwala na precyzyjne wykonywanie otworów i kanałów oraz umożliwia stosowanie różnych grubości materiału.
Inną metodą jest laminacja termiczna, która polega na łączeniu warstw folii miedzianej przy użyciu wysokiej temperatury i ciśnienia. Ta metoda jest idealna dla projektów o dużej gęstości elementów lub wielowarstwowych konstrukcjach.
Kolejną popularną techniką jest drukowanie 3D. Pozwala ona na stworzenie trójwymiarowej struktury płytki drukowanej poprzez nanoszenie kolejnych warstw materiału izolacyjnego i miedziowego. Ta metoda może być stosowana do produkcji małych serii lub pojedynczych egzemplarzy prototypu.
Ostatnią wymienioną tutaj metodą jest fototrawienie, czyli proces chemicznego usuwania niepotrzebnego materiału z płytki drukowanej. Ta metoda jest stosowana głównie do produkcji prototypów o niskiej gęstości elementów lub pojedynczych egzemplarzy.
Jak przebiega proces drukowania ścieżek i nanoszenia warstwy miedzi na podłoże?
Proces drukowania ścieżek i nanoszenia warstwy miedzi na podłoże jest kluczowym etapem w produkcji płytek drukowanych. Pierwszym krokiem jest przygotowanie projektu PCB (Printed Circuit Board), który określa, gdzie mają znajdować się przewody oraz elementy elektroniczne na płytce. Następnie projekt ten zostaje przeniesiony do postaci negatywu.
Kolejnym etapem jest umieszczenie negatywu na specjalnej folii światłoczułej i oświetlenie go promieniami UV. W miejscach, gdzie nie ma przewodów lub elementów, światło utwardza folię, a tam, gdzie są one zaplanowane – nie utwardza jej. Po wyjęciu z procesora fotograficznego powstaje tzw. maska – pozytywny obraz układu druku.
Następnym krokiem jest naniesienie maski na podłoże wykonane z laminatu szklano-epoksydowego pokrytego cienką warstwą miedzi metodą sitodruku lub offsetu. Dzięki temu uzyskuje się wzór odpowiadający planowanemu układowi druku oraz miejsca dla otworów montażowych i innych detali konstrukcyjnych.
Po usunięciu nadmiaru farby pozostawia się płytę w specjalnym roztworze chemicznym rozpuszczającym niewłaściwe fragmenty miedzi. W ten sposób uzyskuje się gotową płytkę drukowaną z naniesionymi ścieżkami i elementami elektronicznymi.
Proces drukowania ścieżek i nanoszenia warstwy miedzi na podłoże jest skomplikowany, ale niezbędny w produkcji płytek drukowanych. Dzięki niemu możliwe jest stworzenie precyzyjnych układów druku, które są wykorzystywane w wielu dziedzinach przemysłu elektronicznego.
Jakie są różne metody montażu komponentów na PCB?
Istnieje wiele różnych metod montażu komponentów na PCB. Jedną z najpopularniejszych jest metoda przewlekana, w której elementy są wprowadzane przez otwory w płycie i lutowane od spodu. Ta metoda jest stosowana głównie do większych elementów, takich jak kondensatory elektrolityczne czy rezystory.
Kolejna popularna metoda to SMT (Surface Mount Technology), która polega na bezpośrednim umieszczeniu elementów na powierzchni płytki i ich lutowaniu przy użyciu pasty lutowniczej oraz pieca lutowniczego. Ta technologia pozwala na bardziej gęste rozmieszczenie elementów i mniejsze rozmiary płytek drukowanych.
Inną metodą montażu jest BGA (Ball Grid Array), gdzie zamiast nóżek, element posiada kulki lutownicze umieszczone pod spodem. Ten sposób montażu wymaga specjalnego sprzętu oraz precyzji podczas procesu lutowania.
W ostatnich latach coraz częściej stosuje się również hybrydowy sposób montażu, łączący zalety obu poprzednich metod – przewlekanej oraz SMT. W tej technologii niektóre większe lub mniej popularne komponenty są nadal montowane tradycyjnym sposobem przez otwory w płytce, a pozostałe drobniejsze umieszczane są bezpośrednio na powierzchni płytki.
Wybór odpowiedniej metody montażu zależy od wielkości elementów, ilości oraz wymagań co do gęstości rozmieszczenia i kosztów produkcji. W każdym przypadku ważne jest jednak precyzyjne wykonanie procesu lutowania, aby zapewnić niezawodność działania urządzenia na długi czas.
Jakie są etapy testowania i inspekcji PCB?
Testowanie i inspekcja PCB to kluczowe etapy w procesie produkcji płytek drukowanych. Pierwszym krokiem jest testowanie elektryczne, które polega na sprawdzeniu poprawności połączeń między elementami oraz ich funkcjonalności. Testy te przeprowadza się za pomocą specjalnych urządzeń, takich jak tester do badania izolacji lub analizator spektralny.
Kolejnym etapem jest wizualna inspekcja PCB pod kątem błędów wykonawczych, takich jak niedoskonałości lutowania czy uszkodzenia mechaniczne. W tym celu wykorzystuje się mikroskopy o dużym powiększeniu oraz kamery cyfrowe umożliwiające dokładną obserwację każdego detalu płytki drukowanej.
Po zakończeniu tych dwóch etapów następuje testowanie parametrów elektrycznych przy użyciu oscyloskopu lub multimetru. Podczas tego procesu mierzone są wartości prądu, napięcia i oporu na poszczególnych elementach płytki drukowanej.
Ostatnim etapem jest programowanie układów scalonych znajdujących się na płytce drukowanej. Programowanie odbywa się za pomocą specjalistycznego oprogramowania dostarczanego przez producenta danego układu scalonego.
Wszystkie te etapy są niezbędne do zapewnienia poprawnego działania płytki drukowanej oraz minimalizacji ryzyka wystąpienia błędów w jej pracy. Dlatego też producenci PCB zawsze dokładają wszelkich starań, aby proces testowania i inspekcji był przeprowadzony na jak najwyższym poziomie.
Jak wygląda proces produkcji masowej PCB, włączając w to wybór metod produkcji, automatyzację i kontrolę jakości?
Proces produkcji masowej PCB jest złożonym procesem, który wymaga wyboru odpowiednich metod produkcji, automatyzacji i kontroli jakości. Pierwszym krokiem w tym procesie jest zaprojektowanie schematu elektrycznego płytki drukowanej oraz wykonanie projektu w oprogramowaniu CAD. Następnie pliki te są przesyłane do fabryki produkującej PCB.
W zależności od wymagań klienta oraz zastosowania płytki drukowanej, można wybrać różne metody produkcji, takie jak: technologia jednostronna lub dwustronna, laminacja wielowarstwowa czy też technologia HDI (High Density Interconnect). W przypadku dużych nakładów produkcyjnych stosuje się automatyzację procesu produkcji za pomocą specjalistycznych maszyn i urządzeń.
Kontrola jakości jest kluczowym elementem całego procesu produkcji masowej PCB. Fabryka musi posiadać odpowiedni sprzęt diagnostyczny do badania parametrów elektrycznych każdego egzemplarza płytki drukowanej oraz systemy wizyjne do sprawdzania poprawności montażu elementów na płytce. Dodatkowo stosuje się testy termiczne oraz mechaniczne celem potwierdzenia trwałości i niezawodności produktu końcowego.
Podsumowując, proces produkcji masowej PCB to skomplikowany proces wymagający precyzji, doświadczenia i wiedzy technicznej. Ważnym elementem jest wybór odpowiednich metod produkcji oraz automatyzacja procesu. Kontrola jakości to kluczowy etap całego procesu, który zapewnia niezawodność i trwałość produktów końcowych.
Jakie są największe wyzwania związane z produkcją PCB, takie jak miniaturyzacja, rosnące wymagania technologiczne i zrównoważony rozwój? Jakie trendy wpływają na rozwój produkcji elektroniki?
Produkcja PCB, czyli płytek drukowanych, to proces wymagający precyzji i zaawansowanej technologii. Jednym z największych wyzwań w produkcji PCB jest miniaturyzacja. Wraz z rozwojem elektroniki coraz mniejsze urządzenia są potrzebne, co oznacza, że płytki drukowane muszą być również mniejsze. To wymaga od producentów większej dokładności i umiejętności pracy na bardzo małych elementach.
Kolejnym wyzwaniem jest rosnące zapotrzebowanie na bardziej zaawansowaną technologicznie produkcję PCB. Coraz więcej urządzeń elektronicznych wymaga specjalistycznych rozwiązań technologicznych w zakresie projektowania i produkowania płyt drukowanych. Producentom trudno nadążać za tymi zmianami i dostosować swoje metody do nowych wymogów.
Zrównoważony rozwój to kolejny aspekt wpływający na produkcję PCB. Procesy produkcyjne generują wiele odpadów oraz zużywają dużo energii i surowców naturalnych. Dlatego też ważne jest dla branży elektronicznej aby działać w sposób przyjazny dla środowiska poprzez stosowanie recyklingu oraz innowacyjnych metod ograniczenia emisji szkodliwych substancji.
Jednym z trendów wpływających na rozwój produkcji elektroniki jest Internet Rzeczy (IoT). Urządzenia zintegrowane w sieci IoT wymagają specjalnych rozwiązań technologicznych, co wpływa na rozwój produkcji PCB. Innym trendem jest rosnące zapotrzebowanie na urządzenia mobilne, takie jak smartfony czy tablety. To z kolei wymaga od producentów płyt drukowanych dostosowania ich do potrzeb rynku.
Wreszcie, coraz większe znaczenie ma także automatyzacja procesów produkcyjnych. Dzięki temu można osiągnąć większą wydajność i dokładność przy mniejszym nakładzie pracy ludzkiej. Jednakże automatyzacja wymaga inwestycji w nowoczesną technologię oraz szkolenia pracowników, aby mogli obsługiwać maszyny i programy komputerowe.