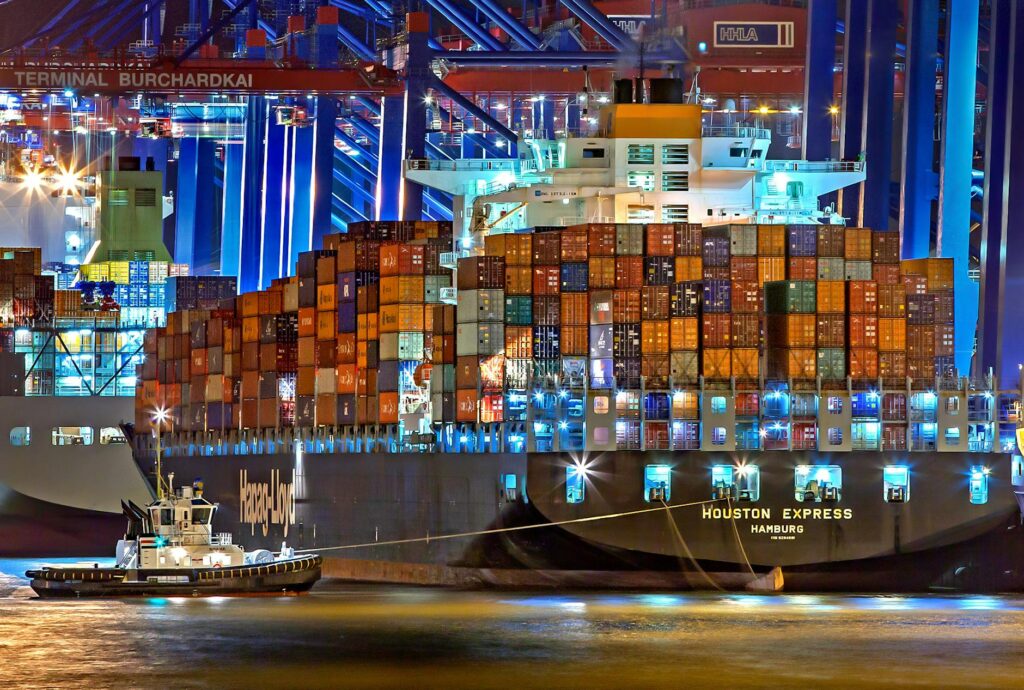
W erze czwartej rewolucji przemysłowej, transformacja tradycyjnych fabryk w inteligentne zakłady produkcyjne staje się kluczowym wyzwaniem dla przedsiębiorców. Integracja nowoczesnych technologii, takich jak Internet Rzeczy (IoT), sztuczna inteligencja i robotyka, nie tylko zwiększa efektywność operacyjną, ale także otwiera nowe możliwości rynkowe. Jak zatem skutecznie wdrożyć te innowacje w istniejącej infrastrukturze, nie zakłócając przy tym bieżącej produkcji? Odpowiedzi na to pytanie szukają zarówno liderzy branży, jak i eksperci technologiczni, którzy podkreślają znaczenie strategicznego planowania i stopniowego wprowadzania zmian.
Znaczenie digitalizacji procesów produkcyjnych dla podniesienia konkurencyjności
Digitalizacja procesów produkcyjnych to kluczowy element, który pozwala firmom zwiększyć swoją konkurencyjność na rynku. Przemysł 4.0 wprowadza nowoczesne technologie, które umożliwiają szybsze i bardziej efektywne zarządzanie zasobami. Dzięki temu przedsiębiorstwa mogą lepiej odpowiadać na zmieniające się potrzeby klientów.
Wprowadzenie cyfrowych rozwiązań pozwala na optymalizację procesów produkcyjnych, co prowadzi do redukcji kosztów operacyjnych. Automatyzacja i monitorowanie produkcji w czasie rzeczywistym pozwala na szybsze reagowanie na problemy oraz minimalizację strat. Firmy, które inwestują w te technologie, zyskują przewagę nad konkurencją.
Integracja nowoczesnych technologii wpływa również na poprawę jakości produktów. Dzięki precyzyjnemu monitorowaniu parametrów produkcji możliwe jest szybkie wykrywanie i eliminowanie błędów. W efekcie klienci otrzymują produkty o wyższej jakości, co przekłada się na ich zadowolenie i lojalność wobec marki.
Przemysł 4.0 umożliwia również lepsze zarządzanie łańcuchem dostaw. Dzięki cyfryzacji możliwe jest śledzenie każdego etapu produkcji oraz dostaw w czasie rzeczywistym. To z kolei pozwala na bardziej precyzyjne planowanie i zarządzanie zasobami, co jest kluczowe w dynamicznie zmieniającym się otoczeniu biznesowym.
Kolejnym istotnym aspektem digitalizacji jest możliwość personalizacji produktów. Nowoczesne technologie pozwalają na elastyczną produkcję, która może być dostosowywana do indywidualnych potrzeb klientów. To z kolei zwiększa atrakcyjność oferty i przyciąga nowych klientów.
Podsumowując, digitalizacja procesów produkcyjnych jest niezbędna dla firm, które chcą utrzymać swoją pozycję na rynku. Inwestycja w nowe technologie przynosi wymierne korzyści w postaci zwiększenia efektywności, redukcji kosztów oraz poprawy jakości produktów. To wszystko przekłada się na wyższą konkurencyjność przedsiębiorstwa.
Jakie nowoczesne technologie automatyzacji warto wprowadzić na linie produkcyjne?
Wprowadzanie nowoczesnych technologii automatyzacji na linie produkcyjne może znacznie poprawić wydajność i efektywność operacyjną przedsiębiorstwa. Jednym z najważniejszych rozwiązań są roboty przemysłowe, które mogą wykonywać powtarzalne zadania z dużą precyzją i szybkością. Dzięki nim możliwe jest znaczne zwiększenie tempa produkcji przy jednoczesnym obniżeniu kosztów pracy.
Kolejną technologią wartą uwagi są systemy automatycznego sterowania, które umożliwiają pełną kontrolę nad procesami produkcyjnymi. Dzięki nim możliwe jest monitorowanie parametrów takich jak temperatura, ciśnienie czy wilgotność w czasie rzeczywistym, co pozwala na szybkie reagowanie na wszelkie odchylenia od normy.
Warto również rozważyć wprowadzenie technologii druku 3D, która umożliwia szybkie prototypowanie oraz produkcję komponentów na żądanie. Druk 3D jest szczególnie przydatny w branżach, gdzie konieczna jest produkcja małych serii produktów lub części zamiennych.
Zastosowanie systemów wizyjnych to kolejna innowacja, która może znacząco poprawić jakość produkcji. Te systemy wykorzystują kamery i oprogramowanie do analizy obrazów, aby wykrywać defekty i zapewniać zgodność produktów z określonymi standardami jakościowymi.
Automatyczne magazyny to technologia, która pozwala na optymalizację zarządzania zapasami. Dzięki nim możliwe jest automatyczne przyjmowanie i wydawanie towarów oraz śledzenie stanów magazynowych w czasie rzeczywistym, co redukuje ryzyko braków lub nadmiarów zapasów.
Wdrożenie tych nowoczesnych technologii automatyzacji wymaga jednak odpowiedniego przygotowania i planowania. Kluczowe jest przeprowadzenie analizy potrzeb przedsiębiorstwa oraz ocena potencjalnych korzyści i kosztów związanych z inwestycją w nowe rozwiązania.
Cyfrowe bliźniaki i ich rola w symulacjach i optymalizacji procesów przemysłowych
Cyfrowe bliźniaki to zaawansowane modele cyfrowe rzeczywistych obiektów lub procesów, które umożliwiają przeprowadzanie symulacji oraz optymalizację procesów przemysłowych. Dzięki nim możliwe jest tworzenie dokładnych odwzorowań fabryk, maszyn czy całych linii produkcyjnych, co pozwala na testowanie różnych scenariuszy bez konieczności ingerencji w rzeczywiste środowisko.
Jednym z głównych zastosowań cyfrowych bliźniaków jest możliwość przewidywania awarii oraz planowania konserwacji prewencyjnej. Analizując dane zebrane przez czujniki umieszczone w maszynach, cyfrowe bliźniaki mogą wskazywać na potencjalne problemy zanim te faktycznie wystąpią. To pozwala na unikanie kosztownych przestojów produkcji.
Dzięki cyfrowym bliźniakom możliwe jest również optymalizowanie procesów produkcyjnych pod kątem zużycia energii czy materiałów. Symulacje pozwalają na identyfikację obszarów, gdzie można osiągnąć oszczędności, co przekłada się na redukcję kosztów operacyjnych oraz bardziej zrównoważoną produkcję.
Kolejnym atutem cyfrowych bliźniaków jest możliwość testowania nowych rozwiązań technologicznych bez ryzyka dla rzeczywistych procesów. Przedsiębiorstwa mogą eksperymentować z różnymi ustawieniami maszyn czy zmieniać parametry produkcji, aby znaleźć najbardziej efektywne rozwiązania.
Cyfrowe bliźniaki odgrywają również ważną rolę w szkoleniu pracowników. Dzięki nim możliwe jest przeprowadzanie symulacji scenariuszy awaryjnych oraz treningu bez ryzyka uszkodzenia sprzętu czy zakłócenia procesu produkcji.
Podsumowując, cyfrowe bliźniaki to narzędzie, które znacząco ułatwia zarządzanie i optymalizację procesów przemysłowych. Ich wdrożenie może przynieść wymierne korzyści w postaci zwiększenia efektywności operacyjnej oraz redukcji kosztów związanych z awariami i zużyciem zasobów.
Jak integracja systemów IoT wpływa na monitorowanie i zarządzanie produkcją?
Integracja systemów IoT (Internet of Things) w przemyśle przynosi szereg korzyści związanych z monitorowaniem i zarządzaniem produkcją. Dzięki połączeniu urządzeń i maszyn z siecią możliwe jest zbieranie i analizowanie danych w czasie rzeczywistym, co pozwala na lepsze podejmowanie decyzji operacyjnych.
Jednym z kluczowych aspektów wykorzystania IoT jest możliwość monitorowania stanu maszyn oraz wykrywania anomalii. Czujniki zamontowane w urządzeniach przesyłają dane o ich pracy do centralnego systemu, który analizuje je pod kątem ewentualnych odchyleń od normy. W ten sposób można szybko reagować na problemy zanim doprowadzą one do awarii.
Dzięki IoT możliwe jest również optymalizowanie zużycia energii oraz innych zasobów. Systemy monitorujące zużycie prądu, gazu czy wody pozwalają na identyfikację obszarów, gdzie można osiągnąć oszczędności. W efekcie firmy mogą zmniejszyć swoje koszty operacyjne oraz wpływ na środowisko naturalne.
Kolejną zaletą integracji IoT jest poprawa logistyki wewnętrznej zakładu. Systemy śledzenia pozwalają na bieżąco monitorować przepływ materiałów i produktów w fabryce, co ułatwia planowanie produkcji oraz zarządzanie zapasami.
IoT wspiera również procesy automatyzacji dzięki możliwości integracji z innymi systemami IT w przedsiębiorstwie. To umożliwia płynną wymianę danych między różnymi działami firmy oraz koordynację działań produkcyjnych, logistycznych czy sprzedażowych.
Podsumowując, integracja systemów IoT znacząco wpływa na poprawę efektywności zarządzania produkcją. Dzięki możliwości monitorowania procesów w czasie rzeczywistym firmy mogą szybciej reagować na problemy, optymalizować zużycie zasobów oraz lepiej planować swoją działalność operacyjną.
Sztuczna inteligencja w analizie danych produkcyjnych – korzyści i wyzwania
Sztuczna inteligencja (SI) odgrywa coraz większą rolę w analizie danych produkcyjnych, oferując szereg korzyści, ale także stawiając przed przedsiębiorstwami nowe wyzwania. Jej zastosowanie pozwala na automatyzację analizy dużych zbiorów danych oraz identyfikację wzorców trudnych do wykrycia przez człowieka.
Dzięki SI możliwe jest przewidywanie awarii maszyn oraz optymalizacja harmonogramu konserwacji prewencyjnej. Algorytmy uczenia maszynowego analizują dane historyczne i bieżące, wskazując potencjalne zagrożenia zanim te faktycznie wystąpią. To pozwala na redukcję kosztownych przestojów produkcji.
Kolejną zaletą sztucznej inteligencji jest możliwość personalizacji produktów oraz elastycznego dostosowywania procesów produkcyjnych do zmieniających się potrzeb rynku. Algorytmy SI analizują dane dotyczące preferencji klientów oraz trendów rynkowych, co umożliwia szybsze reagowanie na zmieniające się wymagania.
Sztuczna inteligencja wspiera również optymalizację procesów logistycznych poprzez analizę danych dotyczących przepływu materiałów oraz surowców. Dzięki temu możliwe jest lepsze planowanie dostaw oraz zarządzanie zapasami, co przekłada się na obniżenie kosztów operacyjnych.
Niemniej jednak wdrożenie SI wiąże się także z pewnymi wyzwaniami. Kluczowym aspektem jest zapewnienie odpowiedniej jakości danych, które będą analizowane przez algorytmy. Niska jakość danych może prowadzić do błędnych wniosków oraz decyzji operacyjnych.
Dodatkowo firmy muszą inwestować w odpowiednią infrastrukturę IT oraz szkolenie pracowników, aby skutecznie wykorzystać potencjał sztucznej inteligencji. Wymaga to zarówno nakładów finansowych, jak i czasu poświęconego na przygotowanie zespołu do pracy z nowymi technologiami.
Jakie kroki należy podjąć, aby zminimalizować ryzyko przestoju produkcji?
Aby zminimalizować ryzyko przestoju produkcji, firmy powinny wdrożyć szereg działań prewencyjnych i organizacyjnych. Przede wszystkim kluczowe jest regularne przeprowadzanie konserwacji maszyn i urządzeń, co pozwala na wykrywanie ewentualnych usterek zanim doprowadzą one do poważniejszych problemów.
Kolejnym krokiem jest wdrożenie systemu monitorowania stanu technicznego maszyn za pomocą czujników IoT. Te urządzenia zbierają dane o pracy maszyn w czasie rzeczywistym, umożliwiając szybką identyfikację anomalii i potencjalnych awarii.
Dobrze zaplanowany harmonogram konserwacji prewencyjnej to podstawa minimalizacji ryzyka przestojów. Warto opracować plan regularnych przeglądów technicznych opartych na danych historycznych oraz zaleceniach producenta sprzętu.
Kolejnym istotnym elementem jest szkolenie pracowników z zakresu obsługi maszyn oraz procedur awaryjnych. Dobrze przygotowany personel może szybko reagować na ewentualne problemy oraz podejmować właściwe działania naprawcze.
Należy również zadbać o odpowiednie zarządzanie zapasami części zamiennych. Posiadanie niezbędnych komponentów na miejscu pozwala na szybką wymianę uszkodzonych elementów i minimalizację czasu przestoju.
Ostatecznie warto rozważyć wdrożenie systemu zarządzania jakością opartego na standardach ISO, który pomoże w ujednoliceniu procedur związanych z utrzymaniem ruchu oraz minimalizacją ryzyka awarii.
Przykłady firm, które z sukcesem przeszły cyfrową transformację produkcji
Cyfrowa transformacja produkcji to proces wymagający zaangażowania całej organizacji, jednak wiele firm udowodniło, że warto podjąć to wyzwanie. Jednym z takich przykładów jest firma Siemens, która dzięki wdrożeniu nowoczesnych technologii Przemysłu 4.0 znacząco zwiększyła swoją efektywność operacyjną oraz jakość produktów.
Kolejnym przykładem sukcesu cyfrowej transformacji jest General Electric (GE), która zastosowała technologie IoT i sztucznej inteligencji do optymalizacji swoich procesów przemysłowych. Dzięki temu GE osiągnęła znaczną redukcję kosztów operacyjnych oraz poprawę wydajności maszyn.
Bosch to kolejna firma, która skutecznie wdrożyła rozwiązania Przemysłu 4.0 w swojej działalności produkcyjnej. Dzięki zastosowaniu cyfrowych bliźniaków Bosch był w stanie zoptymalizować swoje linie produkcyjne pod kątem wydajności oraz zużycia energii.
Niemiecka firma Audi również z powodzeniem przeszła cyfrową transformację swoich zakładów produkcyjnych. Wykorzystując technologie automatyzacji oraz analizy danych, Audi zwiększyło elastyczność swoich procesów produkcyjnych oraz skróciło czas potrzebny na dostosowanie linii do nowych modeli samochodów.
Ciekawym przykładem jest także firma ABB, która wdrożyła zaawansowane systemy monitorowania stanu technicznego maszyn oraz analizy predykcyjnej. Dzięki temu ABB mogła lepiej planować konserwację prewencyjną i minimalizować ryzyko przestojów produkcji.
Tego rodzaju sukcesy pokazują, że cyfrowa transformacja może przynieść wymierne korzyści zarówno pod względem operacyjnym, jak i finansowym. Firmy decydujące się na ten krok mają szansę nie tylko zwiększyć swoją konkurencyjność na rynku, ale także poprawić jakość oferowanych produktów oraz usług.