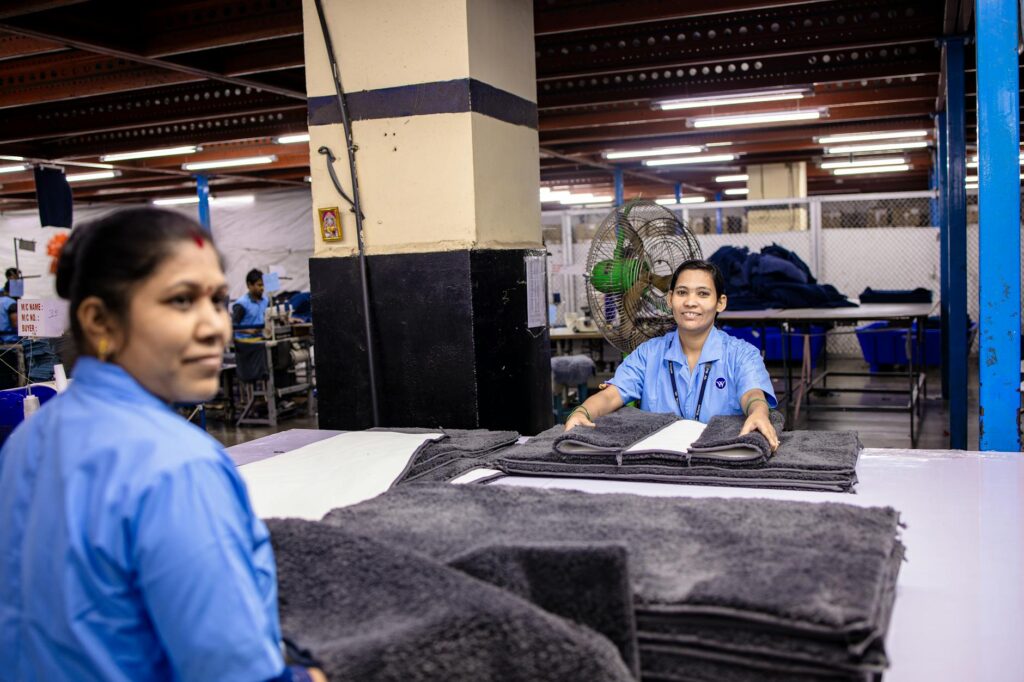
W dzisiejszym dynamicznie zmieniającym się środowisku biznesowym, firmy muszą nieustannie dążyć do zwiększania efektywności swoich procesów produkcyjnych. Kluczem do sukcesu jest nie tylko wdrażanie nowoczesnych technologii, ale także umiejętne zarządzanie zasobami ludzkimi i materiałowymi. Optymalizacja produkcji nie polega jedynie na redukcji kosztów, lecz także na poprawie jakości i elastyczności, co pozwala szybciej reagować na potrzeby rynku. W artykule przedstawimy sprawdzone strategie i narzędzia, które pomogą w zwiększeniu wydajności oraz omówimy, jak unikać typowych pułapek związanych z nadmiernym upraszczaniem procesów.
Jakie technologie wspierają optymalizację procesów produkcyjnych?
Współczesne technologie odgrywają kluczową rolę w optymalizacji procesów produkcyjnych. Jedną z najważniejszych innowacji jest automatyzacja, która pozwala na zwiększenie wydajności i redukcję kosztów operacyjnych. Dzięki automatyzacji można skutecznie zminimalizować błędy ludzkie, co przekłada się na wyższą jakość produktów.
Kolejną technologią wspierającą optymalizację jest Internet Rzeczy (IoT). Urządzenia IoT umożliwiają zbieranie i analizowanie danych w czasie rzeczywistym, co pozwala na szybkie reagowanie na wszelkie nieprawidłowości w procesie produkcyjnym. Dzięki temu możliwe jest również lepsze zarządzanie zasobami i energia.
Systemy ERP (Enterprise Resource Planning) to kolejne narzędzie wspierające optymalizację. Pozwalają one na integrację różnych działów przedsiębiorstwa, co umożliwia bardziej efektywne planowanie i zarządzanie zasobami. Systemy te dostarczają również cennych informacji o stanie produkcji, co ułatwia podejmowanie decyzji.
W kontekście optymalizacji procesów produkcyjnych, nie można zapomnieć o sztucznej inteligencji (AI). AI jest wykorzystywana do analizy dużych zbiorów danych, co pozwala na identyfikację wzorców i przewidywanie potencjalnych problemów. To z kolei umożliwia proaktywne podejście do zarządzania produkcją.
Warto również wspomnieć o drukowaniu 3D, które rewolucjonizuje procesy produkcyjne w wielu branżach. Pozwala ono na szybkie prototypowanie oraz produkcję części na żądanie, co znacznie skraca czas wprowadzenia produktu na rynek i redukuje koszty związane z magazynowaniem.
Ostatecznie, technologie takie jak robotyka znacząco wpływają na optymalizację procesów. Roboty mogą pracować w trudnych warunkach, wykonując zadania z dużą precyzją i szybkością. Dzięki nim możliwe jest zwiększenie wydajności linii produkcyjnych oraz poprawa jakości końcowych produktów.
Jakie narzędzia pozwalają na lepszą organizację pracy w produkcji?
Efektywna organizacja pracy w produkcji wymaga zastosowania odpowiednich narzędzi. Jednym z nich jest system zarządzania projektami, który umożliwia koordynację działań zespołów i monitorowanie postępów prac. Dzięki temu można lepiej planować zasoby i unikać opóźnień.
Kolejnym ważnym narzędziem są harmonogramy produkcji, które pomagają w ustaleniu kolejności działań oraz alokacji zasobów. Harmonogramy te pozwalają na lepsze zarządzanie czasem i redukcję przestojów, co przekłada się na wyższą efektywność całego procesu.
Systemy monitorowania w czasie rzeczywistym to kolejne rozwiązanie, które wspiera organizację pracy w produkcji. Dzięki nim możliwe jest śledzenie stanu maszyn i urządzeń oraz szybkie reagowanie na awarie czy inne nieprzewidziane sytuacje.
Nie można zapomnieć o oprogramowaniu do zarządzania zasobami ludzkimi. Pozwala ono na efektywne planowanie grafiku pracy oraz monitorowanie wydajności pracowników. To narzędzie jest szczególnie przydatne w dużych zakładach produkcyjnych, gdzie zarządzanie zespołami może być wyzwaniem.
Warto również wspomnieć o systemach CRM (Customer Relationship Management), które mogą wspierać organizację pracy poprzez lepsze zarządzanie relacjami z klientami. Dzięki nim możliwe jest lepsze zrozumienie potrzeb klientów oraz dostosowanie procesów produkcyjnych do ich oczekiwań.
Na koniec, narzędzia takie jak tablice kanban wspierają wizualne zarządzanie pracą. Pozwalają one na łatwe śledzenie postępów zadań oraz identyfikację potencjalnych problemów czy opóźnień, co ułatwia podejmowanie szybkich działań naprawczych.
Jakie techniki pomagają w redukcji odpadów w procesach produkcyjnych?
Redukcja odpadów w procesach produkcyjnych jest kluczowa dla zwiększenia efektywności i zrównoważonego rozwoju. Jedną z popularnych technik jest Lean Manufacturing, która koncentruje się na eliminacji marnotrawstwa i optymalizacji przepływu pracy.
Kolejną techniką jest Six Sigma, która wykorzystuje analizy statystyczne do identyfikacji i eliminacji wad w procesach produkcyjnych. Dzięki Six Sigma możliwe jest osiągnięcie wyższej jakości produktów przy jednoczesnej redukcji odpadów.
Recykling materiałów to kolejna metoda redukcji odpadów. Wiele firm wdraża programy recyklingowe, które pozwalają na ponowne wykorzystanie surowców i minimalizację ilości odpadów trafiających na składowiska.
Zastosowanie produkcji just-in-time (JIT) pomaga ograniczyć nadprodukcję i zmniejszyć zapasy magazynowe. Dzięki JIT surowce są dostarczane dokładnie wtedy, gdy są potrzebne, co minimalizuje ryzyko marnotrawstwa.
Niezwykle istotna jest również optymalizacja procesów logistycznych. Poprzez lepsze planowanie tras transportu i efektywniejsze zarządzanie magazynem można znacząco zmniejszyć ilość odpadów generowanych podczas dystrybucji produktów.
Edukacja pracowników na temat znaczenia redukcji odpadów również odgrywa ważną rolę. Świadomi pracownicy są bardziej skłonni do podejmowania działań proekologicznych i zgłaszania pomysłów na dalszą optymalizację procesów produkcyjnych.
Jakie korzyści niesie za sobą analiza wydajności produkcji?
Analiza wydajności produkcji przynosi wiele korzyści dla przedsiębiorstw. Przede wszystkim pozwala na identyfikację obszarów wymagających poprawy, co umożliwia bardziej precyzyjne działania optymalizacyjne.
Dzięki regularnym analizom możliwe jest wczesne wykrywanie problemów, zanim staną się one poważnym zagrożeniem dla ciągłości produkcji. To z kolei przekłada się na mniejsze ryzyko przestojów i awarii maszyn.
Kolejną korzyścią jest możliwość monitorowania postępów. Analiza wydajności pozwala śledzić zmiany w efektywności procesów w czasie, co umożliwia ocenę skuteczności wdrażanych działań naprawczych.
Zwiększenie konkurencyjności to kolejny pozytywny efekt analizy wydajności. Przedsiębiorstwa, które regularnie monitorują swoje procesy, mogą szybciej reagować na zmieniające się warunki rynkowe i lepiej dostosowywać swoją ofertę do potrzeb klientów.
Dzięki analizie wydajności możliwe jest również lepsze zarządzanie zasobami. Znając dokładne potrzeby produkcyjne, firmy mogą optymalizować zużycie surowców i energii, co przekłada się na niższe koszty operacyjne.
Ostatecznie, analiza wydajności pomaga w wzroście satysfakcji klientów. Poprawa jakości produktów i skrócenie czasu realizacji zamówień to czynniki, które mają bezpośredni wpływ na zadowolenie odbiorców końcowych.
Jakie wskaźniki warto monitorować w procesach produkcyjnych?
Monitorowanie odpowiednich wskaźników jest kluczowe dla oceny efektywności procesów produkcyjnych. Jednym z podstawowych wskaźników jest wydajność maszyn, która określa stopień wykorzystania urządzeń w czasie rzeczywistym.
Kolejnym ważnym wskaźnikiem jest współczynnik OEE (Overall Equipment Effectiveness), który mierzy ogólną efektywność maszyn, uwzględniając dostępność, wydajność i jakość produkcji.
Czas cyklu produkcyjnego to kolejny istotny wskaźnik. Mierzy on czas potrzebny na zakończenie jednego cyklu produkcyjnego, co pozwala ocenić tempo pracy linii produkcyjnej.
Należy również monitorować współczynnik odpadów, który informuje o ilości materiału marnowanego podczas procesu produkcyjnego. Wysoki współczynnik odpadów wskazuje na konieczność optymalizacji procesów.
Czas przestoju to kolejny wskaźnik, który warto śledzić. Określa on czas, przez jaki maszyny są nieaktywne z powodu awarii lub konserwacji, co wpływa na ogólną wydajność produkcji.
Ostatecznie, nie można zapominać o współczynniku jakości, który mierzy procent produktów spełniających określone normy jakościowe. Wysoka jakość to klucz do zadowolenia klientów i długofalowego sukcesu firmy.
Optymalizacja produkcji a poprawa jakości produktów
Optymalizacja procesów produkcyjnych ma bezpośredni wpływ na jakość końcowych produktów. Poprzez eliminację marnotrawstwa i lepsze zarządzanie zasobami możliwe jest osiągnięcie wyższej precyzji w procesach wytwarzania.
Dzięki zastosowaniu nowoczesnych technologii, takich jak automatyzacja czy sztuczna inteligencja, możliwe jest dokładniejsze monitorowanie jakości na każdym etapie produkcji. To pozwala na szybkie wykrywanie i korygowanie wszelkich niezgodności.
Kolejnym aspektem wpływającym na jakość jest edukacja pracowników. Świadomi i dobrze przeszkoleni pracownicy są bardziej skłonni do dbania o szczegóły oraz zgłaszania wszelkich problemów jakościowych.
Zastosowanie systemów zarządzania jakością, takich jak ISO 9001, pomaga w utrzymaniu wysokich standardów w całym przedsiębiorstwie. Standardy te definiują procedury i praktyki mające na celu zapewnienie najwyższej jakości produktów.
Dzięki optymalizacji możliwe jest również skrócenie czasu realizacji zamówień bez utraty jakości. Szybsze dostarczanie produktów spełniających oczekiwania klientów przyczynia się do wzrostu ich satysfakcji i lojalności wobec marki.
Należy pamiętać, że jakość produktów to nie tylko ich cechy fizyczne, ale także zgodność z oczekiwaniami klientów oraz normami prawnymi. Dlatego tak ważne jest ciągłe monitorowanie i doskonalenie procesów produkcyjnych w celu spełnienia rosnących wymagań rynku.